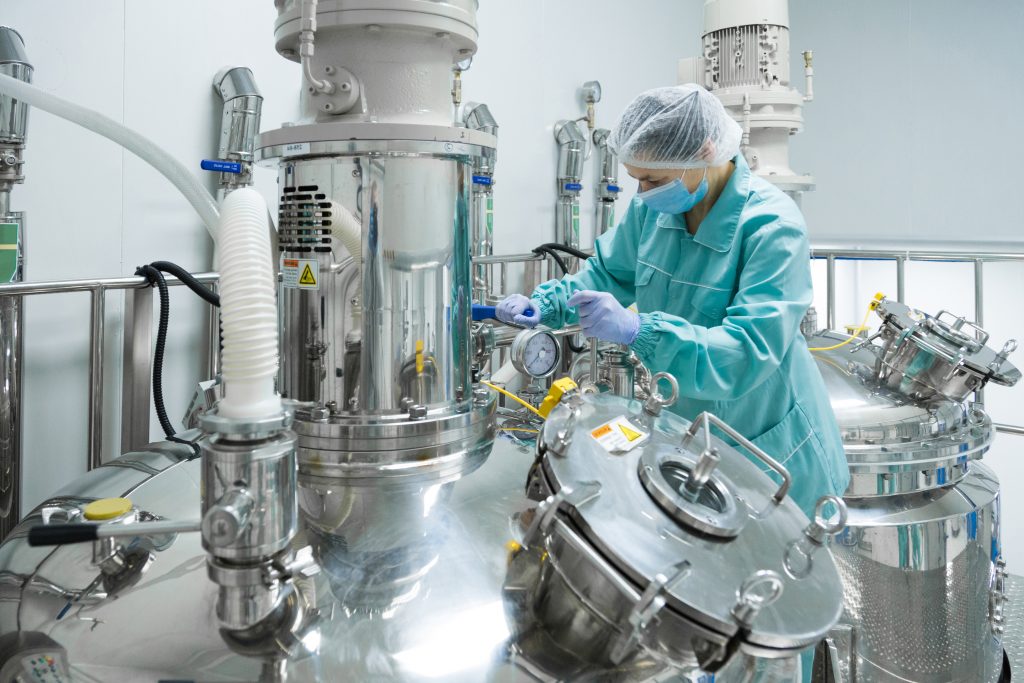
Supply Chain Management in Injectable Manufacturing: Challenges & Solutions
Injectable manufacturing is a critical aspect of the pharmaceutical industry. As the demand for injectable medications continues to rise globally, the supply chain behind their production becomes more complex. Effective supply chain management in injectable manufacturing ensures timely delivery of high-quality products, meeting the growing need for treatments across various healthcare sectors.
The Importance of Supply Chain in Injectable Manufacturing
Injectable medications are used to treat a wide range of conditions, including serious diseases like cancer, infections, and chronic illnesses. These medications are often delivered directly into the bloodstream, making them essential for patients who need immediate or long-term treatment.
The supply chain in injectable manufacturing involves many steps, including sourcing raw materials, production, quality control, packaging, and distribution. Each stage must be carefully managed to ensure the final product meets regulatory standards and reaches healthcare providers on time.
Efficient supply chain management helps reduce the risk of delays, shortages, and quality issues, ensuring that patients receive the care they need without disruption.
Challenges in Supply Chain Management for Injectable Manufacturing
1. Raw Material Shortages
The first step in injectable manufacturing involves sourcing raw materials, such as active pharmaceutical ingredients (APIs) and excipients. The supply of these materials can sometimes be unpredictable due to global supply chain disruptions, natural disasters, or political instability in sourcing regions.
This can lead to delays in production or, worse, prevent the manufacturing process from starting altogether. To mitigate this, injectable manufacturers often have to build relationships with multiple suppliers and keep track of inventory levels.
2. Complex Regulatory Compliance
Injectable medications must meet strict regulatory standards set by health authorities like the CDSCO and FDA. These standards cover everything from the composition of the drugs to their packaging and labeling. Compliance with these regulations is non-negotiable, but it can lead to delays and higher costs.
Injectable manufacturers must constantly stay updated on evolving regulations in different regions. This can be a significant challenge for pharmaceutical companies operating in multiple countries. Navigating this regulatory maze requires dedicated teams and resources to ensure everything is in order.
3. Manufacturing Delays and Bottlenecks
Manufacturing injectables involves highly specialized equipment and processes. Any issues in production, such as equipment failure, contamination, or human error, can lead to delays. These bottlenecks can disrupt the entire supply chain, making it difficult to meet deadlines and demand.
Maintaining a consistent manufacturing process requires constant monitoring, quick decision-making, and preventive maintenance of machinery. Streamlining injectable production processes and eliminating inefficiencies can help reduce delays and ensure smooth operations.
4. Packaging and Labeling Issues
Injectable medications require precise packaging and labeling to ensure patient safety and regulatory compliance. Any mistakes in packaging, labeling, or even storage can compromise the product’s safety, leading to recalls or delays in delivery.
Ensuring that all packaging and labeling processes are accurate is a major challenge. Automation and technology can play a key role in reducing errors and increasing efficiency in this area.
5. Logistical Challenges
Once injectables are manufactured, they must be delivered to healthcare providers and patients. However, logistical issues such as transportation delays, temperature control (for temperature-sensitive medications), and customs clearance can impact timely delivery.
The challenge becomes even greater when products need to be distributed globally. To tackle this, injectable manufacturers often rely on third-party logistics companies that specialize in pharmaceutical transportation, ensuring that products reach their destination safely and on time.
Solutions to Overcome Supply Chain Challenges in Injectable Manufacturing
1. Diversifying Suppliers
To avoid raw material shortages, injectable manufacturers can diversify their suppliers. This means having backup suppliers in different regions, reducing the reliance on one single source. By maintaining a network of suppliers, pharmaceutical companies can reduce the impact of supply chain disruptions.
2. Adopting Lean Manufacturing Practices
Lean manufacturing aims to reduce waste and boost efficiency. By streamlining production processes, pharma companies can reduce delays and bottlenecks. Continuous improvement is key to eliminating inefficiencies and maintaining consistent production levels.
Automating certain production processes, such as filling and labeling, can also improve efficiency. Automation reduces human errors, speeds up production, and ensures more consistent quality.
3. Implementing Advanced Technology
Advanced technologies such as artificial intelligence (AI) and the Internet of Things (IoT) can play a significant role in managing the supply chain. AI can help forecast demand, optimize inventory levels, and identify potential supply chain disruptions before they happen. IoT can be used to track shipments, monitor the condition of products in transit, and ensure that temperature-sensitive injectables remain at the correct temperature.
4. Ensuring Robust Quality Control
Quality control is a critical aspect of injectable manufacturing. By investing in modern testing equipment and procedures, injectable manufacturers can ensure that the final product meets the required standards. A strict quality control system helps prevent delays caused by faulty products and ensures compliance with regulatory requirements.
5. Collaborating with Third-Party Logistics Providers
As injectable manufacturing companies expand globally, managing logistics becomes more complex. Partnering with experienced third-party logistics (3PL) providers can streamline the distribution process. 3PLs specialize in handling pharmaceutical products and are equipped to handle the unique requirements of injectable medications, including temperature control and compliance with global regulations.
Armein Pharmaceuticals: Leading Injectable Manufacturers in India
In the heart of India, Armein Pharmaceuticals shines as a leader in the world of injectable production. With a state-of-the-art facility spanning 250,000 sq. ft., we specialize in producing high-quality parenteral products. Our commitment to quality is evident in our advanced laboratories and stringent quality control measures. By adhering to WHO GMP and PIC/S standards, Armein Pharmaceuticals ensures that every product meets the highest safety and efficacy benchmarks.
Moreover, our strategic location in Gujarat allows us to efficiently serve both domestic and international markets, including Asia, Africa, Latin America, and the CIS countries. Our team’s dedication to transforming healthcare with precision and care makes us a trusted partner in the pharmaceutical industry.
Conclusion
Managing the supply chain in injectable manufacturing is a complex but essential task. By addressing challenges such as raw material shortages, regulatory compliance, and logistical issues, injectable manufacturers can ensure the timely delivery of high-quality injectables. Implementing solutions like diversifying suppliers, adopting lean manufacturing, and leveraging advanced technology can help overcome these challenges.
With pharma companies like Armein Pharmaceuticals leading the way, the industry continues to evolve, providing safe and effective treatments to patients worldwide.
FAQs
How can injectable manufacturers minimize production downtime?
Regular maintenance and timely replacement of equipment, along with continuous monitoring, can help minimize production downtime and ensure smooth operations.
What impact does temperature control have on injectable product quality?
Temperature control is crucial for maintaining the stability and efficacy of temperature-sensitive injectables, ensuring they remain safe for patient use.
Why is diversification of suppliers crucial for injectable manufacturers?
Diversifying suppliers helps reduce dependency on a single source, mitigating risks posed by supply chain disruptions like natural disasters or political instability.
What role do packaging innovations play in improving injectable supply chains?
Packaging innovations, like tamper-evident seals and temperature-sensitive labels, enhance product safety, reduce errors, and streamline logistics, improving overall supply chain efficiency.
How can predictive analytics improve the injectable supply chain?
Predictive analytics can forecast demand trends, identify potential disruptions, and optimize inventory management, ensuring that injectable manufacturers can meet market needs without overstocking or understocking.
How can injectable manufacturers ensure product traceability?
By implementing serialization and barcoding systems, manufacturers can track products at every stage of the supply chain, improving traceability, accountability, and regulatory compliance.