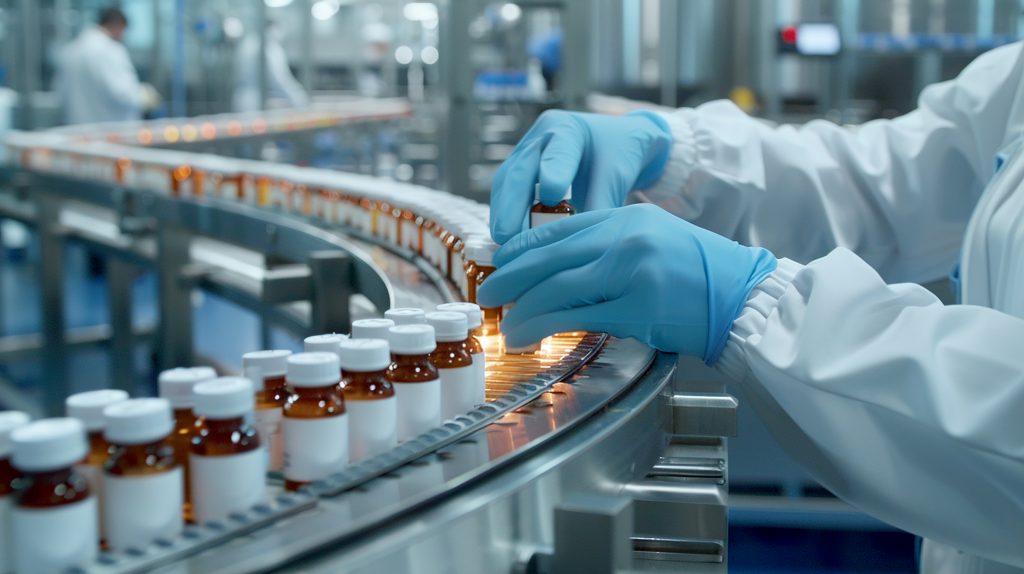
Lyophilization Efficiency: How Pharma Manufacturers Accelerate Small-Molecule Injectable Production.
In the fast-evolving world of sterile injectables, pharma manufacturers are under immense pressure to produce safe, stable, and scalable medications with speed and precision. Among the many innovations transforming this space, lyophilization, commonly known as freeze-drying, has emerged as a game-changer.
For small-molecule injectable drugs, where heat sensitivity and stability are critical concerns, lyophilization ensures product longevity without compromising efficacy.
This blog explores how leading pharma manufacturers, including Armein Pharmaceuticals, are optimizing lyophilization to accelerate the production of lyophilized injectables, meeting global demand while ensuring quality, compliance, and innovation.
Why Lyophilization is Crucial for Injectable Manufacturing
Lyophilization is a specialized process where water is removed from a product after it is frozen and placed under a vacuum, allowing ice to change directly from solid to vapour. This method is vital for injectables that are heat-sensitive or require extended shelf life.
For pharma manufacturers, the benefits of lyophilization include:
- Improved product stability and shelf life.
- Enhanced solubility for reconstitution.
- Safe transport under non-refrigerated conditions.
- Preservation of active pharmaceutical ingredients (APIs) without chemical degradation.
These advantages are particularly crucial for injection manufacturers in India, where climatic conditions and export requirements demand enhanced drug resilience and sterility.
Understanding the Lyophilization Process
The typical freeze-drying cycle involves:
- Freezing – The injectable solution is frozen, locking its structure.
- Primary Drying (Sublimation) – Under vacuum, the ice turns into vapour without becoming liquid.
- Secondary Drying (Desorption) – Residual moisture is removed, stabilizing the final product.
Armein Pharmaceuticals has fine-tuned this multi-step process through advanced automation and validation, making us a leading injectable manufacturer trusted globally.
Challenges Faced by Pharma Manufacturers in Lyophilization
Despite its benefits, lyophilization presents several challenges:
- Long cycle times (often up to 72 hours per batch).
- High energy consumption.
- Complex process validation and temperature sensitivity.
- Equipment costs and maintenance for large-scale production.
For pharma manufacturers, overcoming these hurdles without compromising sterility, potency, or scalability requires continuous innovation, something Armein is known for.
Armein’s Breakthroughs in Lyophilization Efficiency
As one of the most forward-thinking injection manufacturers in India, Armein Pharmaceuticals has built a robust framework to accelerate and optimize lyophilization:
1. Advanced Lyophilizers
Armein employs fully automated lyophilization systems with:
- SCADA-based control systems
- Shelf temperature and chamber pressure monitoring
- Clean-in-place (CIP) and steam-in-place (SIP) integrations
- Vial stoppering under vacuum to maintain aseptic conditions
2. AI-Powered Cycle Optimization
Using machine learning, Armein shortens lyophilization cycles by predicting optimal sublimation rates, product collapse temperature thresholds, and endpoint detection.
3. Seamless Integration with Cleanroom Environments
Each lyophilizer is integrated into Grade A cleanrooms, ensuring aseptic processing and zero contamination.
This approach helps Armein, as a top-tier injectable manufacturer, deliver consistent quality at scale, reducing production time without sacrificing compliance.
Small-Molecule Focus: The Real-World Impact
Lyophilization is particularly vital for small-molecule injectables used in:
- Oncology
- Anesthesia
- CNS disorders
- Gastrointestinal and anti-infective therapies
Armein’s expertise as one of the trusted pharma manufacturers shines through its product offerings in this space.
Notable Lyophilized Injectables by Armein:
- Esomeprazole Lyophilized 40 mg – for acid reflux and gastric ulcers.
- Cerebroprotein Hydrolysate Lyophilized 60 mg – for neurological recovery.
- Olanzapine Lyophilized 10 mg – antipsychotic for schizophrenia and bipolar disorder.
These lyophilized injectables meet stringent international guidelines and are exported to 15+ countries, including Latin America, Africa, and Southeast Asia.
Why Injection Manufacturers in India are Embracing Lyophilization
India has emerged as a hub for sterile injectable production. Among injection manufacturers in India, lyophilization has gained momentum due to:
- Rising demand from global health agencies (e.g., WHO, UNICEF).
- Cost competitiveness and capacity for large-scale production.
- Increased prevalence of diseases requiring heat-sensitive injectable therapies.
With GMP-certified facilities and a focus on innovation, pharma manufacturers like Armein are setting new benchmarks in reliability and efficiency.
Quality Assurance and Regulatory Alignment
Lyophilization must adhere to strict guidelines from:
- WHO-GMP
- PIC/S
- EU-GMP
- CDSCO India
- ISO 13485
Armein’s in-house QA/RA teams conduct continuous monitoring, validation, and documentation across every freeze-drying cycle. The company’s track record in regulatory inspections underpins its status as a preferred injectable manufacturer across regulated and semi-regulated markets.
Sustainability in Lyophilization
Sustainability is no longer optional for pharma manufacturers. Armein has taken proactive steps to reduce the environmental impact of freeze-drying:
- Energy-efficient compressors and heat-exchange systems.
- Closed-loop water systems to minimise waste.
- Eco-friendly packaging and labelling for lyophilized injectables.
These measures support Armein’s mission to be not only a leader in healthcare but also in responsible manufacturing.
What the Future Holds: Next-Gen Freeze-Drying
Innovation in lyophilization continues to evolve. Key trends include:
- Continuous Lyophilization – reducing cycle times dramatically.
- 3D-Printed Vial Holders – for precision heat transfer.
- Pre-Filled Lyophilized Syringes – merging convenience and sterility.
- IoT-enabled monitoring – real-time data collection for preventive maintenance.
As technology advances, pharma manufacturers that embrace intelligent systems will lead the charge in small-molecule delivery systems.
Why Armein Leads Among Pharma Manufacturers
Armein Pharmaceuticals stands out for its:
- Dedicated sterile injectable infrastructure
- Expertise in both terminal sterilization and aseptic lyophilization
- Export reach to over 15 countries
- R&D efforts in advanced drug delivery
Whether it’s launching high-impact lyophilized injectables or serving as a reliable injectable manufacturer for global health programs, Armein continues to push boundaries.
Conclusion: Accelerating Global Healthcare through Lyophilization
Lyophilization is more than a technical process; it’s a critical capability that empowers pharma manufacturers to deliver reliable, life-saving medications across borders.
As demand for small-molecule injectables grows, manufacturers like Armein are leveraging smarter systems, AI optimization, and cleanroom precision to lead the next wave of healthcare delivery. Through our innovations in lyophilization, Armein remains a trusted partner in global health.
Explore Further
Want to know more about Armein’s sterile injectable capabilities and lyophilized solutions?
Explore our manufacturing facilities
See our full product list