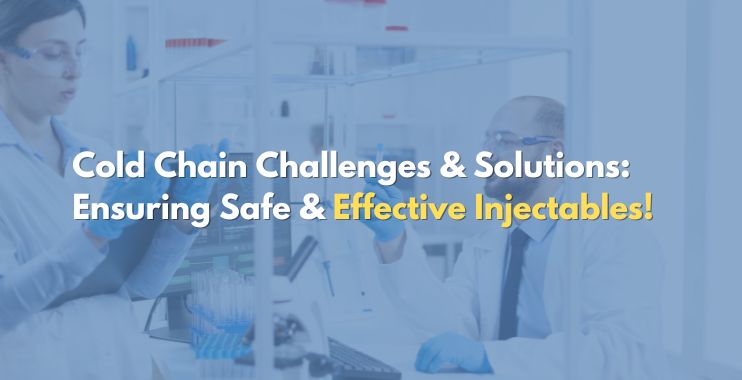
Challenges and Solutions in Cold Chain Management for Injectable Pharmaceutical Companies
Injectables are a vital part of modern medicine. They save lives, treat chronic illnesses, and improve the quality of healthcare worldwide. However, producing injectables isn’t as straightforward as mixing ingredients and packing them up.
One of the most critical steps pharmaceutical companies have to go through in this process is cold chain management. This highly intricate system ensures injectables are stored, transported, and distributed at precise temperatures to maintain their potency and safety. Sounds simple? It’s far from it.
Cold chain management for injectables manufacturing comes with unique challenges. Let’s break them down and explore how pharmaceutical companies in India, like Armein Pharmaceuticals, are solving them with innovation and expertise.
Challenge 1: Temperature Sensitivity
Pharmaceutical companies in India often manufacture injectables from biological materials, which are highly sensitive to temperature changes. A minor fluctuation, whether too cold or too warm, can make a batch ineffective or even dangerous. The stakes are incredibly high, as spoiled products can lead to treatment failures and health risks.
Solution: Advanced Monitoring Systems
To tackle this, pharma manufacturers now use smart temperature sensors. These devices track temperature levels in real-time, ensuring strict compliance with storage requirements. Armein Pharmaceuticals uses state-of-the-art IoT-based technology. Our system alerts teams immediately if temperature variations occur during transit or storage, preventing potential losses.
Challenge 2: Complex Logistics
Imagine shipping life-saving medicines across continents. Every link in the supply chain, from pharma manufacturers to pharma distributors, must keep the injectable at the right temperature. But things like customs delays, power outages, or transportation breakdowns can disrupt the cold chain. A single weak link and the entire effort collapses.
Solution: Specialized Packaging and Transport
One effective approach is the use of insulated shipping containers and refrigerants. These containers maintain stable conditions for long durations. Armein Pharmaceuticals partners with trusted logistics companies to ensure timely delivery. Our cold storage vehicles are equipped with GPS tracking and temperature control, guaranteeing that products reach their destinations safely.
Challenge 3: Regulatory Compliance
Different countries have varying rules for cold chain management. Pharmaceutical companies must meet stringent guidelines for temperature control, packaging, and documentation. Falling short could result in delays, penalties, or even product recalls.
Solution: Robust Documentation and Automation
Many pharmaceutical companies rely on automated systems to stay compliant. These systems maintain detailed logs of temperature data, shipping times, and other critical metrics. Armein Pharmaceuticals goes a step further by conducting routine compliance checks and training our staff on international cold chain regulations. Our proactive approach ensures that products are always shipped with zero hiccups.
Challenge 4: High Operational Costs
Running a cold chain system is expensive. Equipment maintenance, energy consumption, and specialized training for personnel all add up. For small and medium pharma manufacturers, these costs can be overwhelming.
Solution: Energy-Efficient Innovations
Energy-efficient refrigerators and solar-powered cold storage units are game-changers. They not only cut down costs but also reduce environmental impact. The leading pharmaceutical companies in India invest in these sustainable technologies, ensuring they deliver quality without breaking the bank.
Challenge 5: Limited Infrastructure in Remote Areas
In some regions, especially rural or remote areas, maintaining a cold chain can be almost impossible. Limited electricity, poor roads, and a lack of storage facilities create significant barriers for pharma manufacturers in India.
Solution: Community-Driven Cold Chains
Pharmaceutical companies collaborate with local governments and NGOs to build cold storage units in underserved areas. Armein Pharmaceuticals leads such initiatives in India. Our community-focused approach ensures even the remotest corners have access to life-saving injectables, reinforcing our commitment to better healthcare.
Challenge 6: Risk of Contamination
When injectables aren’t stored correctly, contamination risks rise. It could be due to improper sealing, exposure to harmful bacteria, or chemical degradation caused by fluctuating temperatures.
Solution: Quality Checks at Every Stage
Regular quality checks by pharmaceutical companies can help prevent contamination. Armein Pharmaceuticals implements rigorous testing at every step, from production to packaging. Our labs use advanced techniques to identify potential risks early, ensuring only the safest products reach the market.
Challenge 7: Limited Awareness Among Stakeholders
Cold chain management isn’t just the pharma manufacturer’s responsibility. Pharmaceutical distributors, healthcare workers, and even end-users play a part in maintaining product integrity. However, a lack of awareness can lead to mishandling.
Solution: Education and Training
Workshops, digital guides, and awareness campaigns go a long way in addressing this issue. The leading pharmaceutical companies in India frequently organize training programs for healthcare professionals. These sessions cover proper storage practices, handling guidelines, and the importance of maintaining cold chains.
Why Armein Pharmaceuticals Stands Out
In the vast field of pharmaceutical companies, Armein Pharmaceuticals has emerged as a leader in injectable manufacturing in India. We don’t just meet industry standards, we set them.
With years of experience, cutting-edge technology, and a patient-first approach, we at Armein Pharmaceuticals have mastered cold chain management. Our commitment to quality and innovation ensures that life-saving injectables reach patients in perfect condition, no matter the challenges.
Looking Ahead: The Future of Cold Chain Management
The Indian pharmaceutical industry is evolving rapidly. With advancements in AI and blockchain, cold chain management is expected to become even more efficient. AI can predict risks like weather-related disruptions or equipment failures. Blockchain ensures full transparency by tracking products at every stage, reducing the risk of tampering.
Armein Pharmaceuticals is already exploring these technologies to stay ahead of the curve. By combining innovation with expertise, we aim to redefine how injectables are manufactured and distributed.
Conclusion
Cold chain management might sound like a behind-the-scenes process, but its impact is enormous. Without it, millions of patients would lose access to critical treatments. While challenges are significant, pharmaceutical companies like Armein Pharmaceuticals prove that solutions are always within reach.
By focusing on innovation, sustainability, and community outreach, the pharmaceutical industry is creating a safer and healthier future. With reliable cold chains, we can ensure that every injectable does what it’s meant to – save lives.
FAQs About Cold Chain Management for Injectables Manufacturing
What is cold chain management in pharmaceuticals?
Cold chain management involves maintaining specific temperature ranges to store, transport, and distribute temperature-sensitive medicines like injectables. It ensures the products remain safe and effective until they reach patients.
Why are injectables so sensitive to temperature changes?
Injectables often contain biological materials that degrade when exposed to unsuitable temperatures. Even a slight fluctuation can reduce their potency or make them unsafe for use.
What is the ideal temperature range for storing injectables?
The ideal temperature range depends on the product. Most injectables require storage between 2°C and 8°C. Some specialized products may require freezing temperatures or ultra-cold conditions.
What happens if the cold chain is broken?
Breaking the cold chain can lead to product spoilage, contamination, or reduced efficacy. These compromised products can pose serious health risks to patients and result in financial losses for pharmaceutical companies.